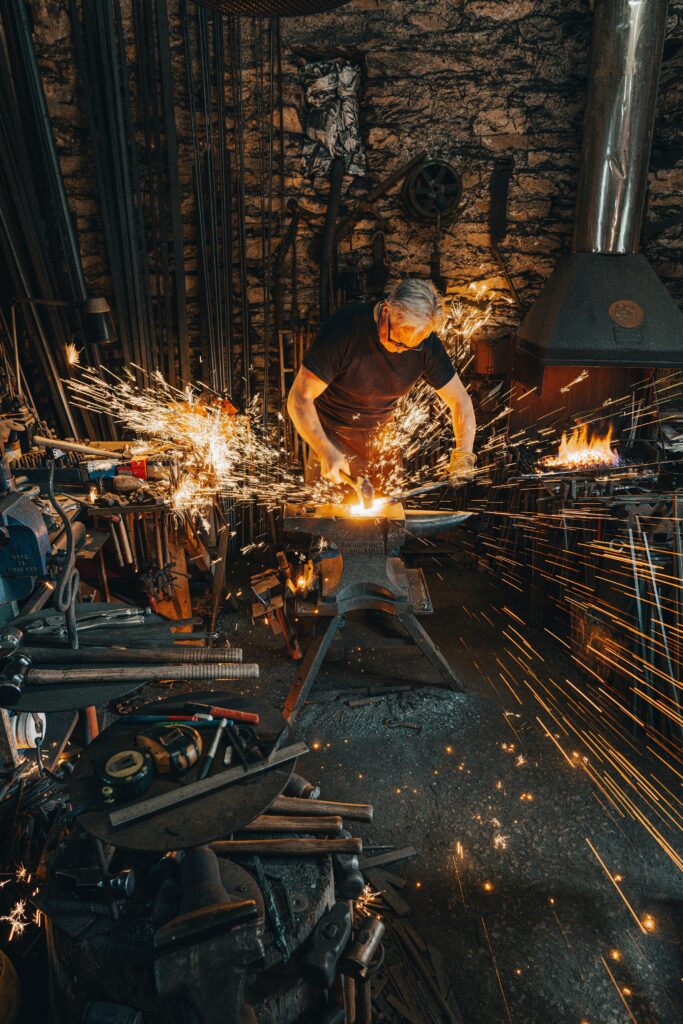
The Bamburgh Sword was far more than a weapon. It was a 7th century work of art rivalling the Lindisfarne Gospels. It was a statement of intent and an announcement of its owner as a superior warrior – and one likely to kill you.
The technology required to make the Bamburgh Sword, and similar pattern-welded weapons, was staggering. The finest bog ore was smelted to make iron and steel.
Then the iron was forged into regularly twisted bars which were welded together to form a perfect chevron pattern and the basic sword shape was formed. The very finest blades had wootz (crucible steel) added to reduce imperfections in the material.
The steel edge was welded to the core. The iron core made the sword flexible and fluid in the hand. The steel edge made the blade wickedly sharp. It was the interplay between iron and steel that was the key to the success of these magical blades.
The blade was fullered and ground to shape. The entire blade was heated and quenched several times to normalise. Then it was heated and quenched in water or brine. At this point the metal was brittle, so it was reheated to a lower temperature and allowed to cool slowly.
The final step: sharpening.